Henry Ford was not the first to create the assembly line, but his car and moving assembly line were certainly the most successful and memorable.
After creating his version of the automobile in 1896, Ford moved workshops first to Mack Avenue and later to Piquette Avenue in Detroit.
These first two factories were small-scale structures for limited car production. Only in 1913 at Ford’s third factory at Highland Park did mass production begin on a truly large scale.
As shown in these rare photographs, Ford applied assembly line methods throughout the factory to all aspects of car production. The resulting productivity gains and price cuts led manufacturers of every type to adopt Ford’s innovative production methods.
In 1907, Henry Ford announced his goal for the Ford Motor Company: to create “a motor car for the great multitude.” At that time, automobiles were expensive, custom-made machines.
Ford’s engineers took the first step toward this goal by designing the Model T, a simple, sturdy car, offering no factory options, not even a choice of color.
Model T was built to be durable for service on the rough American country roads of that period, economical to operate, and easy to maintain and repair. It was first put on the market in 1908, and more than 15 million were built before it was discontinued in 1927.
From the start, the Model T was less expensive than most other cars, but it was still not attainable for the “multitude.”
Ford realized he’d need a more efficient way to produce the car in order to lower the price. He and his team looked at other industries and found four principles that would further their goal: interchangeable parts, continuous flow, division of labor, and reducing wasted effort.
Using interchangeable parts meant making the individual pieces of the car the same every time. That way any valve would fit any engine, any steering wheel would fit any chassis.
This meant improving the machinery and cutting tools used to make the parts. But once the machines were adjusted, a low-skilled laborer could operate them, replacing the skilled craftsperson who formerly made the parts by hand.
To improve the flow of the work, it needed to be arranged so that as one task was finished, another began, with minimum time spent in set-up. Ford was inspired by the meat-packing houses of Chicago and a grain mill conveyor belt he had seen.
If he brought the work to the workers, they spent less time moving about. Then he divided the labor by breaking the assembly of the Model T into 84 distinct steps.
Each worker was trained to do just one of these steps. Ford called in Frederick Taylor, the creator of “scientific management,” to do time and motion studies to determine the exact speed at which the work should proceed and the exact motions workers should use to accomplish their tasks.
Ford’s assembly technique consisted of two basic elements: a conveyor system and the limitation of each worker to a single repetitive task. Despite its deceptive simplicity, the technique required elaborate planning and synchronization.
As a result, Ford’s cars came off the line in three-minute intervals, much faster than previous methods, reducing production time from 12 hours before to 93 minutes by 1914, while using less manpower.
In 1914, Ford produced more cars than all other automakers combined. The Model T was a great commercial success, and by the time Ford made its 10 millionth car, half of all cars in the world were Fords.
It was so successful Ford did not purchase any advertising between 1917 and 1923; instead, the Model T became so famous, people considered it a norm.
More than 15 million Model Ts were manufactured in all, reaching a rate of 9,000 to 10,000 cars a day in 1925, or 2 million annually, more than any other model of its day, at a price of just $260 ($4,017 today).
The Ford Model T was named the most influential car of the 20th century in the 1999 Car of the Century competition, ahead of the BMC Mini, Citroën DS, and Volkswagen Beetle.
Ford’s Model T was successful not only because it provided inexpensive transportation on a massive scale, but also because the car signified innovation for the rising middle class and became a powerful symbol of the United States’ age of modernization.
Ford had another notion, rather original in its time: the workers were also potential consumers. In 1914, Ford workers’ wages were raised to $5 a day, an excellent wage, and they soon proved him right by buying their own Model Ts.
Ford was called “a traitor to his class” by other industrialists and professionals, but he held firm in believing that well-paid workers would put up with dull work, be loyal, and buy his cars.
Not only did Henry Ford increase the wages of his employees, but he also decreased the number of hours they were responsible for working. Henry Ford decreased the shifts by one hour and gave employees higher wages.
The shift length decrease allowed Ford to create a third shift and hire more workers. The assembly allowed Ford Motor Company to become a twenty-four-hour operation.
“Fordism” also grew out of the moving assembly line. Fordism refers to large-scale production combined with higher wages, and it spread to other industries following the $5 day started by Ford Motor Company.
This move by Ford was followed by other companies and changed the business and manufacturing world across the nation as workers began to seek out jobs that came with higher wages and shorter hours.

Automobile chassis on the way to final assembly, 1925.
Ford’s success inspired imitation and competition, but his primacy remained unchallenged until he lost it in the mid-1920s by refusing to recognize that the Model T had become outmoded.
More luxurious and better-styled cars appeared at prices not much higher than that of the Model T, and these were increasingly available to low-income purchasers through a growing used-car market.
In Britain, William R. Morris (later Lord Nuffield) undertook to emulate Ford as early as 1912, but he found British engineering firms reluctant to commit themselves to the large-scale manufacture of automotive parts.
Morris in fact turned to the United States for his parts, but these early efforts were cut short by World War I. In the 1920s Morris resumed the production of low-priced cars, along with his British competitor Herbert Austin and André-Gustave Citroën and Louis Renault in France.
British manufacturers had to face the problem of a tax on horsepower, calculated on a formula based on bore and the number of cylinders.
The effect was to encourage the design of small engines that had cylinders with narrow bore and long stroke, in contrast to the wide-bore, short-stroke engines favored elsewhere. This design handicapped the sale of British cars abroad and kept production from growing.
Although the appearance of mass production in the automotive industry coincided with the emergence of large-scale business organization, the two had originated independently.
They were related, however, and influenced each other as the industry expanded. Only a large firm could make the heavy investment in plant and tooling that the assembly line required, and Ford was already the largest single American producer when it introduced the technique.
The mass producer in turn enjoyed a cost advantage that tended to make it increasingly difficult for smaller competitors to survive. There have been exceptions, but the trend has been consistent.

Building the body of an automobile, 1916.

Factory workers on Ford assembly line for bearings, 1924.

Finished auto bodies.

A trunk line conveyor in 1924.
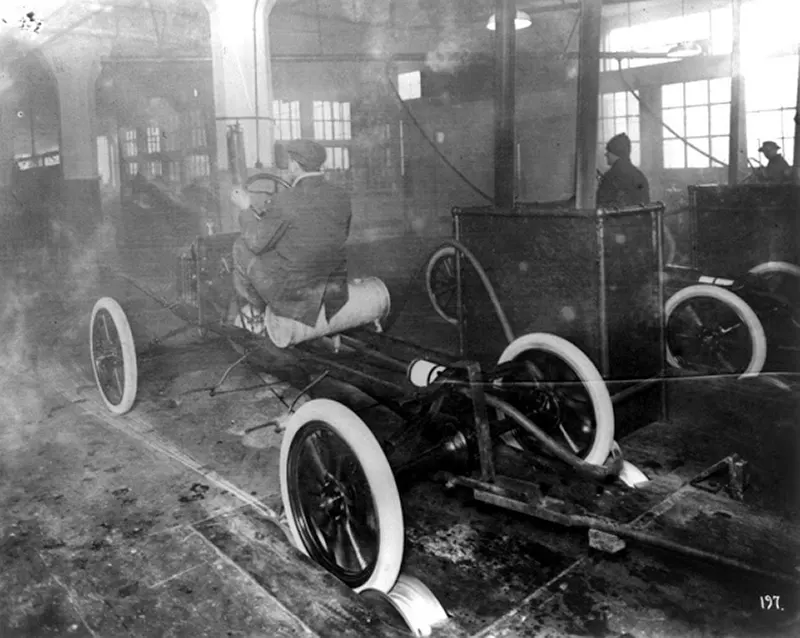
Model Ts coming off the assembly line at the Highland Park plant.
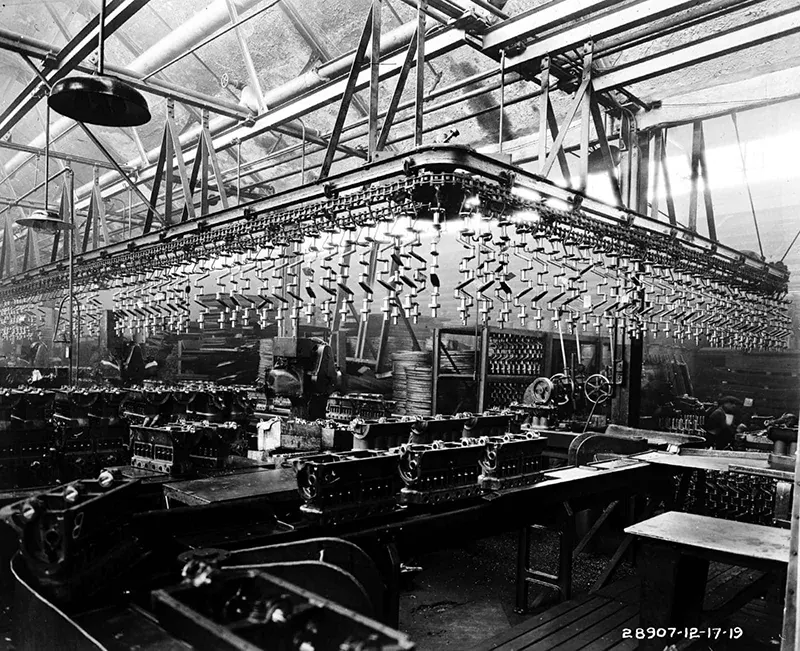
Motor blocks ready for assembly, 1919.
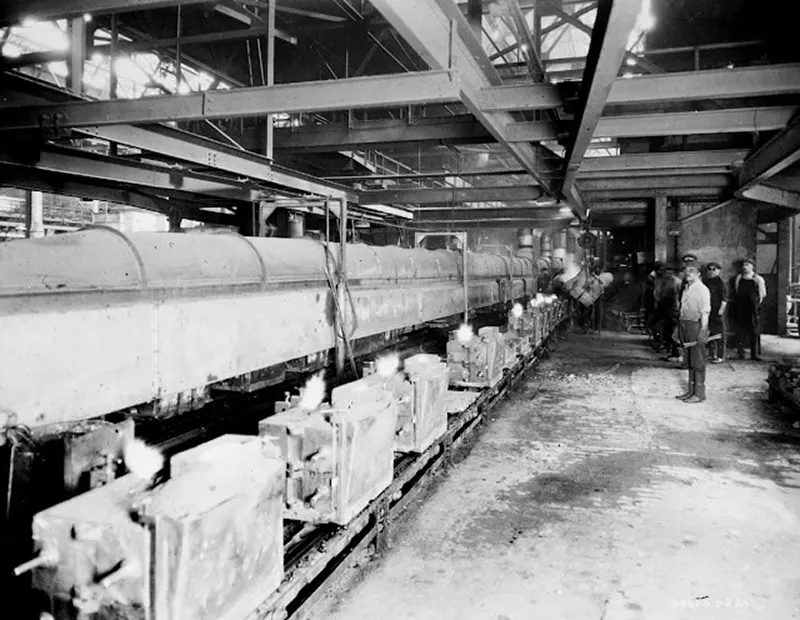
The conveyor bringing the molds, 1924.

Working on the doors.

Assembling door locks.
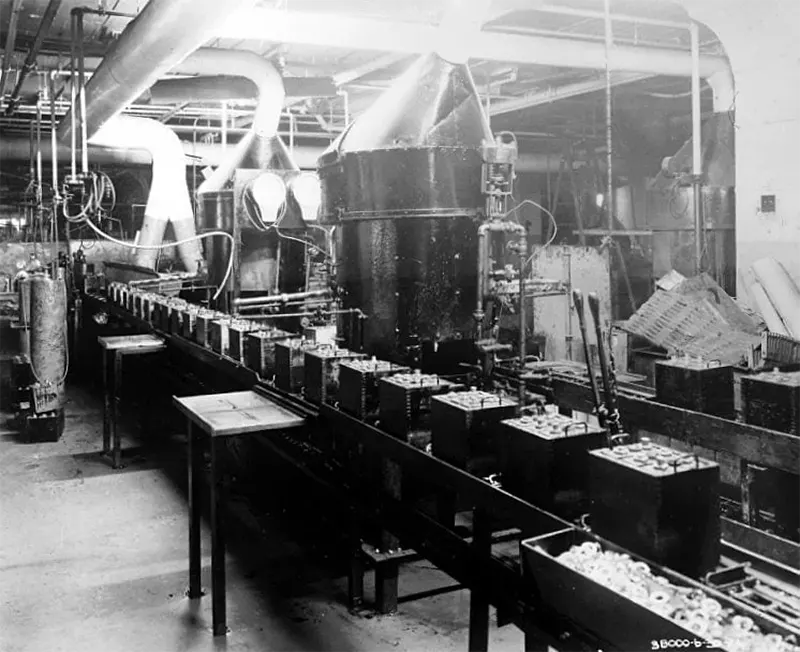
Batteries on conveyor, 1924.
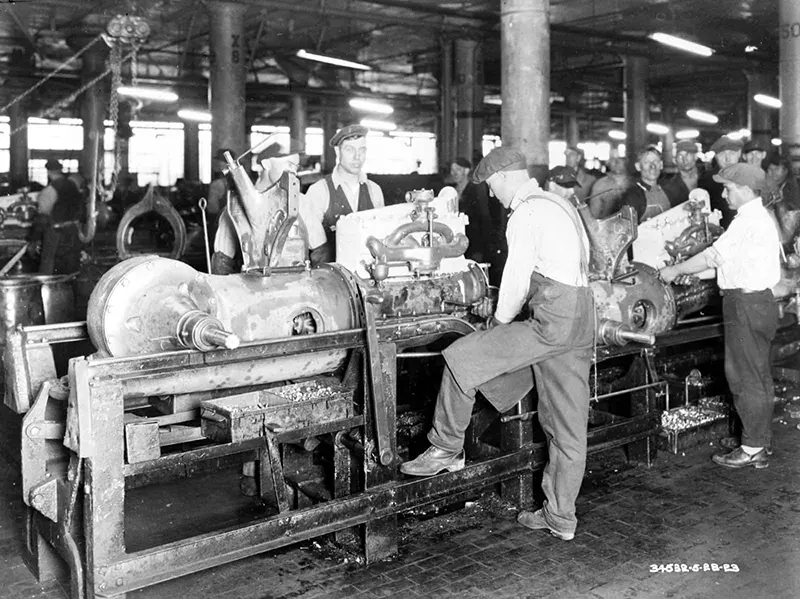
Installing a motor, 1923.

Working on the transmission.
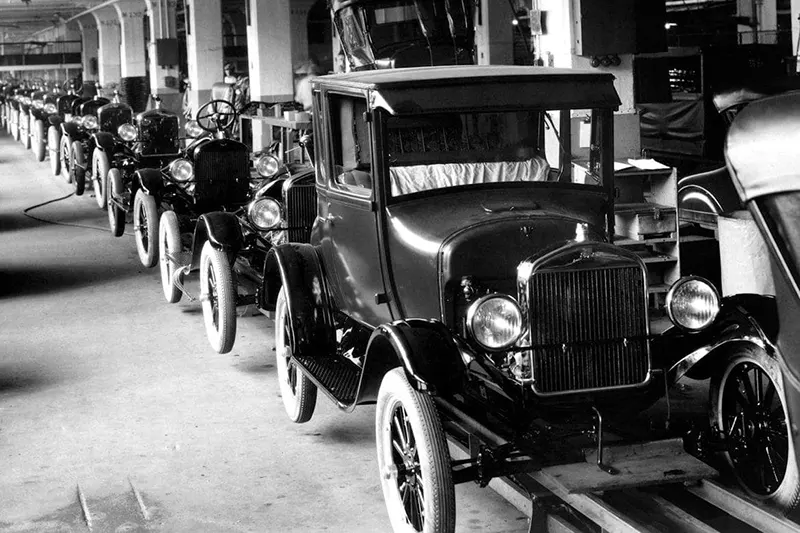
Ford Model T assembly line, 1926.

Ford Motor delivery department.
(Photo credit: From the collection of Henry Ford / Flickr / Britannica )